AAC Inc personnel have helped their clients with:
- Maintenance Parts Management Assessments (and Initiative Prioritization)
- Maintenance Parts Management Optimization programs
- Leading Practices Training (See the Change Management and Education section)
- Maintenance Parts Management Detailed support for:
- Systems Requirements development;
- Inventory Planning /Policy Training;
- Inventory Optimization Facilitation;
- Logistics Requirements Development;
- Maintenance Parts KPI/Metric Development;
- Asset Lifecycle Alignment Spare Parts List creation;
- Reliability Centered Maintenance Training (RCM2/3); and
- Re-Thinking Maintenance Parts Processes.
Maintenance Parts Management – Strategy
Asset Acumen Consulting Inc. has a proven method for:
- Spare Parts Management Assessment, initiative prioritization and
- Strategy Development Facilitation Services.
Asset Acumen Consulting Inc. has a proven method for:
- Determining your current spare parts capabilities baseline;
- Providing your organization with an understanding of where you are in your corporate maturity of the maintenance parts management continuum;
- Presenting a calibrated standard of Leading Practices in Maintenance Parts Management and an understanding of your desired future state;
- Coaching of your organization’s current Parts operation and Asset Lifecycle in support of Maintenance Parts; and
- Developing a prioritized initiative (tasks) and plans for an improvement roadmap for their Parts Management support programs.
Asset Acumen Consulting Inc. helps clients identify their current level of Maintenance Parts Management maturity, prioritize opportunities/initiatives, and develop a roadmap for change that can be executed by their cross-functional teams (Maintenance and Operations working together).
Maintenance Parts Management – Asset Life cycle
Total asset life-cycle management (ALM) includes a life cycle for each part (or item) that is in the composition of each asset in an asset life cycle. It should include consideration for an inventory stocking policy from parts acquisition to its eventual parts disposal or disposition. ALM would include costs for the initial asset purchase and related initial spares purchases required to support an asset installation, repair, replacement, upgrade, and movement to and from repair facilities (if applicable). As well, the removal from service, dismantling, and disposal should be considered at the time of design and costing out the total cost of ownership (TCO).
Asset Acumen Consulting Inc. assists organizations to get their Asset Life-cycle role model defined or reset for their organization. Significant savings can be gained by getting the organization aligned to get an optimal return from its’ their assets. Their asset support should be also aligned to their strategic reason for having the asset and supporting their strategic business model.
Maintenance Parts Management – Metrics
Fundamental Maintenance Parts Management metrics may be considered a fairly simple task to put together. Often recommended asset metrics will include measuring: parts fulfillment/availability, parts quality, inventory values, or inventory turnover and losses. Getting the whole organization on the same page and supporting each level of the business (Strategy, Operational, Functional,) and the priority pendulum of business drivers dynamically is typically a more complex exercise to work through.
- Key Performance Metrics for Maintenance Parts Management involves:
- An approach to tailoring KPIs for multiple business dimension levels
- Examples of maintenance parts operational, and inventory effectiveness KPIs
- Developing a balanced scorecard for a maintenance parts operation
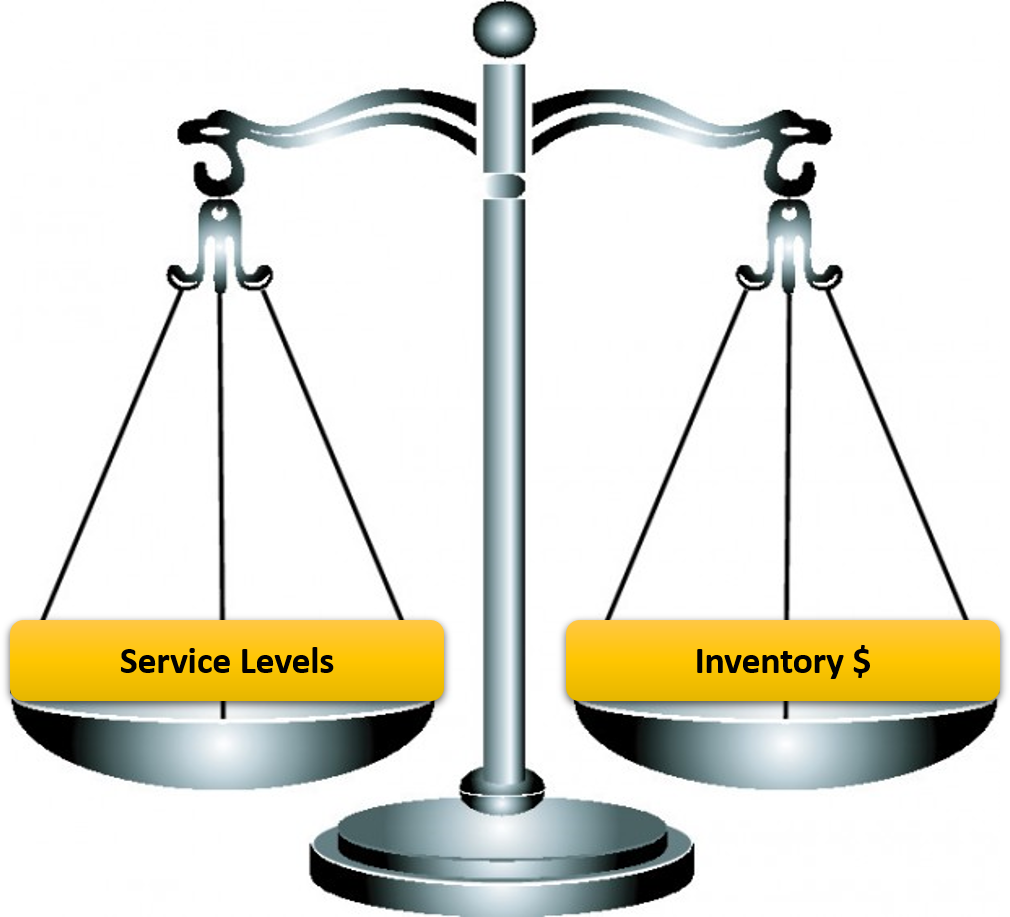
Organizations Business Reputation
Key Performance Indicators
- Parts Availability
- Parts Acquisition Time
- Systems Availability
- Distribution Quality
- Parts Quality
- Parts Costs
- Inventory Turnover
- Inventory Reserves
Asset Acumen Consulting Inc. helps organizations work through the maze of potential focus areas to help them to identify the needed (and available) maintenance parts-related metrics and prioritize based on the business strategic and operational dynamic.